- In the pharmaceutical industry, the parts of vibrating screens that come into contact with materials mostly use 304 or 316L stainless steel, which has excellent corrosion resistance, ensuring that drugs are not contaminated and meeting strict pharmaceutical hygiene standards. In terms of screening accuracy, relying on fine screens and precise vibration settings, it can strictly grade raw materials and drugs according to the requirements of the pharmacopoeia, ensuring the uniformity of particle size. Its hygienic design is ingenious, with a smooth interior and no dead corners, making it easy to clean, effectively preventing the growth of bacteria and the residue of materials. It has strong operational stability and can operate continuously for a long time, reducing the risk of shutdown due to failures. With a low-noise design, it creates a quiet production environment, comprehensively assisting in the efficient and safe production of pharmaceuticals.
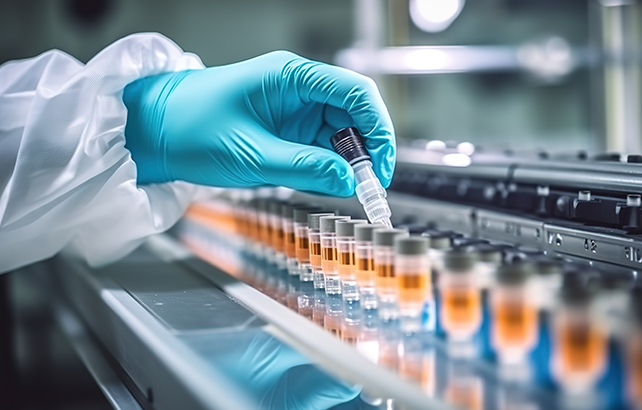
Applications in the pharmaceutical industry
Vibrating screens in the pharmaceutical industry are mainly used for operations such as screening, grading, impurity removal, and filtration of various pharmaceutical raw materials, intermediates, finished pharmaceutical preparations, etc., and play a crucial role in the pharmaceutical industry. The following are some materials commonly applied to vibrating screens in the pharmaceutical industry:
- Active Pharmaceutical Ingredients (APIs)
- Pharmaceutical Intermediates
- Traditional Chinese Medicine Powder
- Traditional Chinese Medicine Liquid
- Traditional Chinese Medicine Pills
- Chinese Herbal Medicine
- Titanium Dioxide
- Lactose
- Pharmaceutical Sugar
- Sucrose
- Tricalcium Phosphate
- Calcium Phosphate
- Potassium Phosphate
- Sodium Bicarbonate
- Magnesium Silicate
- Mannitol
- Sorbitol
- Glycerol
- Magnesium Stearate
- Nucleotide
- Zinc Gluconate
Recommended screening equipment
In the pharmaceutical industry, vibrating screens must strictly adhere to the quality management specifications during the production process to ensure the quality and safety of drugs. In terms of materials, the entire machine is made of stainless steel of grade 304 or higher, and the components in contact with the materials must be guaranteed to be free of impurities and pollution. Accessories such as seals and bouncing balls need to be made of medical-grade silicone material to prevent material contamination caused by aging and cracking.
The structural design of the equipment should avoid sanitary dead corners and be easy to disassemble, assemble and clean. The surface needs to be finely polished to achieve smoothness and cleanliness, without black spots or burrs. Before leaving the factory, it is necessary to thoroughly clean and disinfect the equipment with professional medical disinfectants. In addition, for pharmaceutical materials with flammable and explosive characteristics, explosion-proof vibrating motors should be equipped to avoid production accidents.